While most people ski on snow that nature has provided only during winter, mSnow defies nature with its synthetic snow surface, allowing people to ski, tube and snowboard year-round. With its proven durability in more than 50 ramp installations, mSnow surfaces are made from 95 percent recycled road construction barrels.
The beginning
Twin brothers Adam and Luke Schrab – co-owners of Plastisnow, LLC in Plainwell, Mich. – co-founded mSnow in 2010.
Adam and Luke grew up as avid skiers in the Midwest (primarily in Wisconsin, Michigan, and Minnesota) and traveled to numerous freestyle skiing competitions. After a short career in upright and inverted aerial competition at the national level (Adam was the national upright aerials champion in 1998), they landed roles in four Warren Miller ski films.
“Our reason for launching mSnow was that we wanted to build synthetic summer water ramp training kickers, but couldn’t get our hands on any sliding surface, especially on a budget and on such a small scale,” said Luke. “Fifteen years [traveling] to ski areas and 15 years of work in ski area operations have been the impetus for rigorously testing and developing mSnow.”
Luke says a big part of their preparation for the inverted aerial competition involved training at the Utah Olympic Sports Park. This facility operates full-size synthetic summer training kickers where skiers slide down a surface of plastic ski bristles.
“This early version of snow surface – originally produced in Canada – is no longer produced. Our mSnow product is similar in design, with numerous high-tech improvements, given all the technological advances available in the world of plastics. We are both degreed engineers and used our industrial experience to design and engineer mSnow.”
mSnow production
Essentially, mSnow is a bristled tile approximately one inch in height. A blend of industrial recycled plastics and orange road construction barrels goes into mSnow production.
“We reclaim plastics, wash them and then process them in plastic shredding equipment,” said Luke. “After that, the shredded plastic gets blended with additives that improve slipperiness, freezing-cold weather durability and UV resistance. Finally, the product is produced through an injection molding process.”
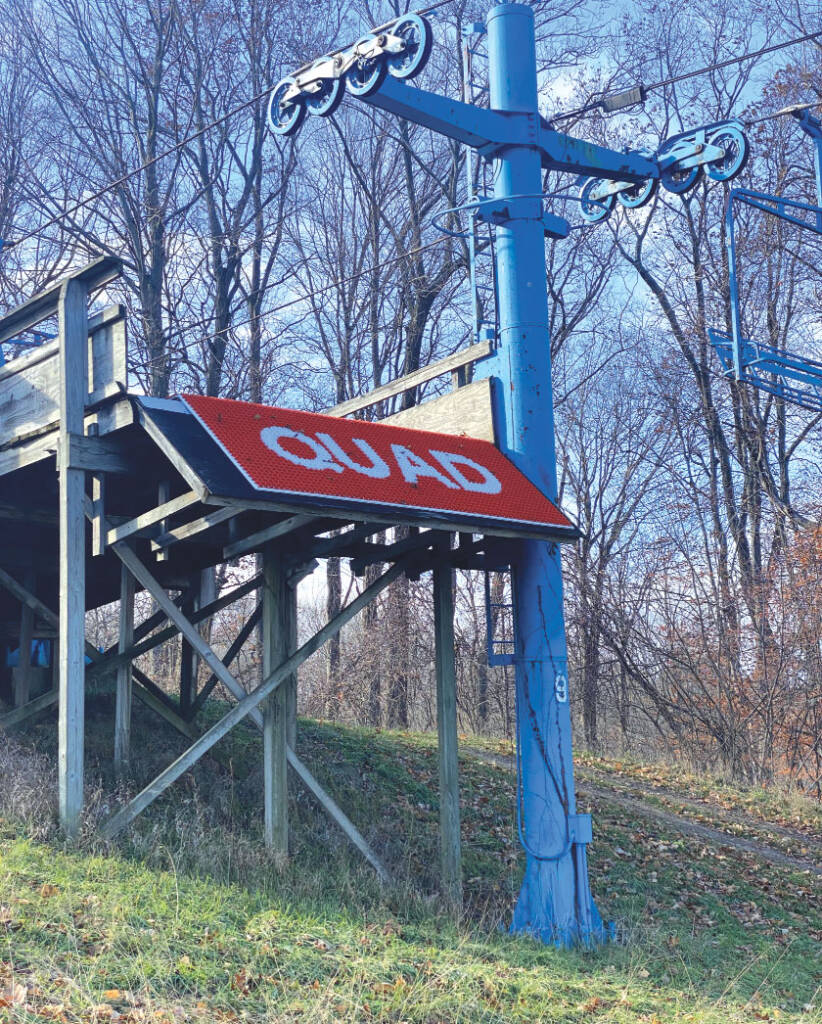
Although mSnow technically allows for loading and unloading a lift with no snow, snow naturally builds up on load and unload ramps.
“The mSnow itself is very durable and can survive very [freezing-cold] temperatures, even heavy ice buildup, although we don’t recommend chipping ice away with shovels as the plastic can be damaged,” he said.
“The snow fills in the bristles, and then throughout the ski day, the operators rake back the snow down to the bristle height. This process improves guests’ experience due to the flat chairlift load and unload zones.”
The consistency of ramps across the mountain and the reduced shoveling and operator maintenance requirements allow the operators to focus more on safe loading and unloading, and interacting with guests as they use the lifts.
Types of mSnow
Commercial white mSnow is a super durable artificial ski surface engineered for the most demanding outdoor year-round applications. Features include:
- Low coefficient of friction
- Maximum UV resistance
- Cold cracking resistance to -30°F
- Pure white color
- Two-year guarantee in most applications
- Expected lifespan of more than five years (depending on the level of use)
- Custom color matching available
- Fully recyclable
- Made in Michigan
Recycled orange mSnow is extremely tough, long-lasting and made from recycled orange construction barrels. It is recommended for most freestyle ramp applications. Features include:
- Engineered for commercial use on loading ramps
- Differs from the backyard orange mSnow
- Low coefficient of friction
- Maximum UV resistance
- Cold cracking resistance to minus -30°F
- High-visibility orange
- It can be used for high-contrast borders on white installations
- Two-year guarantee in most applications
- Expected lifespan of more than five years (depending on the level of use)
- Made from at least 75 percent recycled plastic
- Fully recyclable
- Made in Michigan
Luke says the primary costs involve the reclamation of used plastics, washing and shredding, additives and the injecting molding process.
“Interestingly, our efforts in developing recycling procedures have allowed us to be more immune to supply chain and raw material scarcity issues. Although recycling plastics minimizes raw material use and is very good for the Earth in that it minimizes waste, it doesn’t happen without some effort and financial cost.”
Numerous ski resorts use mSnow
More than 100 ski areas in 20 U.S. states and four Canadian provinces use mSnow at their 500-plus lift ramps. Depending on the number of uses and weather exposure, it typically lasts five to 10 years on a lift ramp.
“Its durability is fully qualified as each year we have as many repeat customers as we do new customers,” said Luke.
Additionally, the company has more than 1,000 backyard customers unrelated to the ski areas that use it.
“These kids build their own small backyard setups where they practice rails and jumps with skis and snowboards.”
What’s next?
As for the future of mSnow over the next three to five years, the company is starting to expand its uses for mSnow. This includes actively testing and developing the product for services such as conveyor load and unload platforms, snowmobile paths into buildings or trailers, lift operator standing zones (anti-slip winter surface), ski-in/ski-out areas to buildings and covered areas and more.
Luke says the company will continue its strong recycling efforts.
“We have started to recycle our own product with a few pilot customers. These customers like our product enough to replace the old mSnow with our new, better blends. We offer them a recycling credit towards a future invoice when we recover the used mSnow. This credit is usually enough to cover the shipping cost of the new order. We plan to expand on this program to make it streamlined enough to offer to all our customers.”